Are you fed up with aimlessly working without accomplishing your desired results? Well, buckle up because success is all about delivering outcomes. And the secret to achieving what you want lies in the effectiveness of Kanban metrics.
Kanban flow metrics offer a window into your team’s workflow, help you identify where improvements can be made, and let you know where your priorities should be. For instance, with Kanban metrics like lead time and work-in-progress adherence, you can gather the data needed to make informed decisions and get desired results.
But how can you use metric reporting to increase your goal completion rate? And which Kanban metrics should you even use? Let’s take a look at Kanban metrics, understand where and how to use them, and why using the Kanban method is crucial when improving workflows.
What Are Kanban Metrics?
Kanban flow metrics are key performance indicators (KPIs) used to measure your team’s performance using the Kanban method. They also give insights into the areas where your team may need improvement and help you deliver large and complex projects without failing.
Think of it like this: if you’re driving a car without a gas gauge or a speedometer, you won’t be able to determine how fast you are going or how much fuel is left. But if your car has a gas gauge, you can understand how much fuel you’re using and take appropriate action if a leak happens.
We can use the same concept with Kanban metrics, as without these KPIs, even if your team is working hard, they wouldn’t be able to track their progress or look into the areas that need improvement.
But that doesn’t mean Kanban metrics only target areas of improvement. In fact, Kanban metrics are tailored to measure different aspects of progress. For instance, cycle time evaluates the time it takes a task from start to finish.
Similarly, lead time measures the total time taken from task initiation to completion. So, using the right metric at the right time is crucial if you want to make workflow improvements.
How to Measure Kanban Performance?
Kanban performance can be measured using various methods and metrics. These metrics can provide valuable insights into the efficiency and effectiveness of the system.
But the exact methods and metrics used will depend on the specific requirements and goals of the organization and the unique characteristics of the Kanban system. However, you can start with the following process:

- Look for the most critical metrics for your team and projects. This may include cycle time to evaluate the completion speed, work-in-progress limits to measure the task being done at once, etc.
- Start tracking your Kanban metrics after successfully identifying them. You can either do this manually or use personalized software. It all depends on the size of your team and how complex your work tasks are.
- Analyze and review the data being collected. This may involve monthly or weekly meetings to evaluate performance or discuss performance to set new goals.
- Use insights from your tracked metrics to improve processes, drive success and prioritize tasks. This could improve small adjustments to workflows, implement new technologies or reallocate resources.
If we put it all together, measuring Kanban performance is about tracking the right metrics, improving processes, and analyzing the data.
What Are Key Metrics to Manage a Kanban Workflow?
Using the Kanban method will give you better insights into tracking performance, prioritizing tasks, and improving continuously. However, with so many metrics, it can be challenging to know where to start.
Let’s look at key metrics used to manage a Kanban workflow:
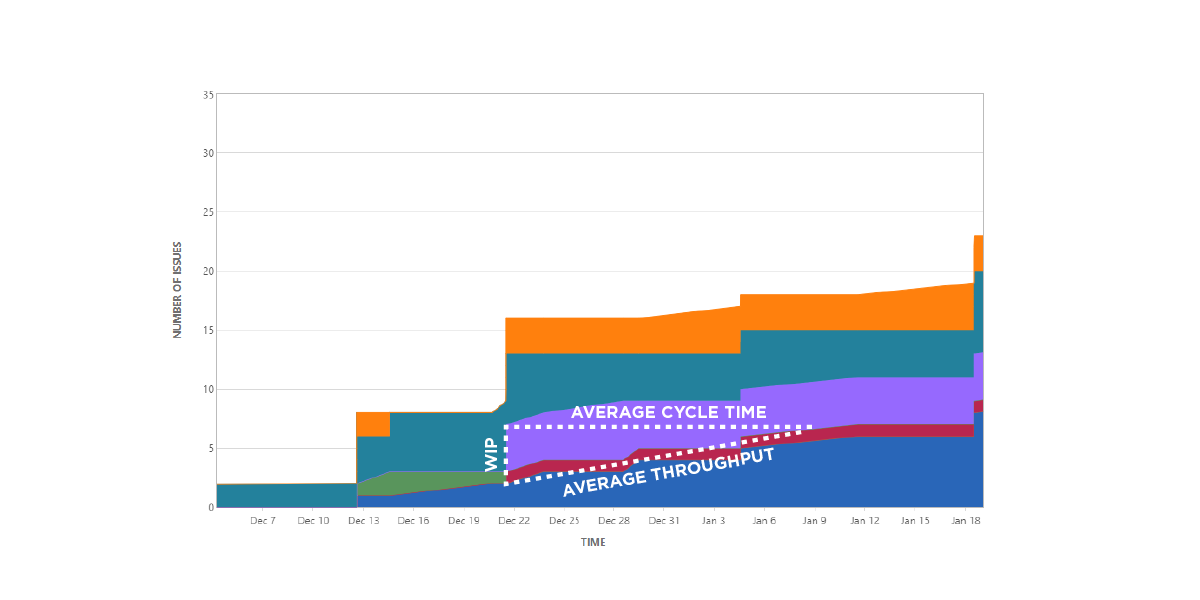
1. Cycle Time
Cycle time measures the amount of time it takes for a task or work item to move through each stage in a process or workflow. It’s an important measure of efficiency, as it provides insight into the speed at which work is being completed and identifies any bottlenecks or areas for improvement.
However, it’s crucial to remember cycle time isn’t merely about speed. The metric takes account of your task complexity and the resources available. It helps to improve visibility into the efficiency of the processes and workflows, leading to more informed decision-making.
This project management metric can also be used to establish a baseline for future projects and to track progress over time. This helps to identify trends and areas where the processes can be continuously improved.
Plus, cycle time can be used to set realistic delivery time expectations and to monitor performance against those expectations, ensuring that projects are delivered on time and to a high standard.
2. Lead Time
Lead time is a project management metric that measures the total time it takes for a task or work item to move from when it enters the system to when it’s delivered. It provides insights into the speed at which work is being completed and helps to identify any bottlenecks or areas for improvement.
So, a high lead time means it took more than expected time for your team to complete the tasks and hints at bottlenecks. In contrast, a low lead time refers to high process efficiency and indicates everything is running smoothly.
By using the lead time metric, you can evaluate your team’s performance and responsiveness. It also helps in achieving the full potential of your team and projects. So, lead time is a critical metric for ensuring that projects are delivered on time and to a high standard.
3. Work in Progress (WIP)
Work in Progress (WIP) refers to the number of tasks or work items currently being worked on within a system, process, or workflow. In a Kanban workflow, WIP is an important concept as it helps to limit the amount of multitasking that occurs and ensures that tasks are completed efficiently.
By limiting WIP, teams can focus on delivering high-quality outputs, reducing lead times, and increasing overall productivity. WIP limits also help to reduce the risk of overloading the system, which can lead to bottlenecks and delays in delivery.
Plus, limiting WIP helps to identify areas for improvement, such as the need for additional resources or process changes.
Moreover, by monitoring WIP levels and keeping them within established limits, teams can focus on delivering high-quality work, increasing productivity, reducing the risk of bottlenecks and delays, and making data-driven decisions to optimize the workflow, ensuring that projects are delivered on time.
4. Team Throughput
Team throughput evaluates how much work your team can handle in a given time. In other words, it measures the amount of work your team completes at a respective time. It doesn’t track work in progress.
By measuring the amount of work the team can complete in a given time period, managers can identify areas for improvement and make data-driven decisions to optimize the workflow, increasing productivity, reducing lead times, and improving the quality of outputs.
Plus, tracking team throughput helps to identify trends over time and can provide valuable insights into the capacity of the team and the resources they need to complete tasks effectively. These insights can be used to make informed decisions about staffing, allocation of resources, and process improvements.
Moreover, tracking team throughput also helps to prioritize work and make data-driven decisions about which tasks should be given priority in the workflow. This can lead to better alignment of resources with organizational goals and ensure that the most important work is completed first.
A throughput histogram is used to calculate the team throughput. The histogram assists in calculating the tasks completed by your team in a period and evaluates your team’s capacity. When you know the number of tasks completed over time, you can decide whether you want to expand your team to complete the projects promptly.
5. Flow Efficiency
Flow efficiency measures the effectiveness of a workflow. It’s calculated by dividing the amount of value-added work by the total amount of work processed through the system. The metric is expressed as a percentage.
This Kanban metric helps identify workflow areas that are slowing down the process, generating waste, or creating inefficiencies. By tracking flow efficiency, organizations can make data-driven decisions to optimize workflow and improve the delivery of projects.
Moreover, the metric can help to reduce lead times, limit waste, increase customer satisfaction, and ensure that projects are delivered on time.
6. Cumulative Flow Diagram
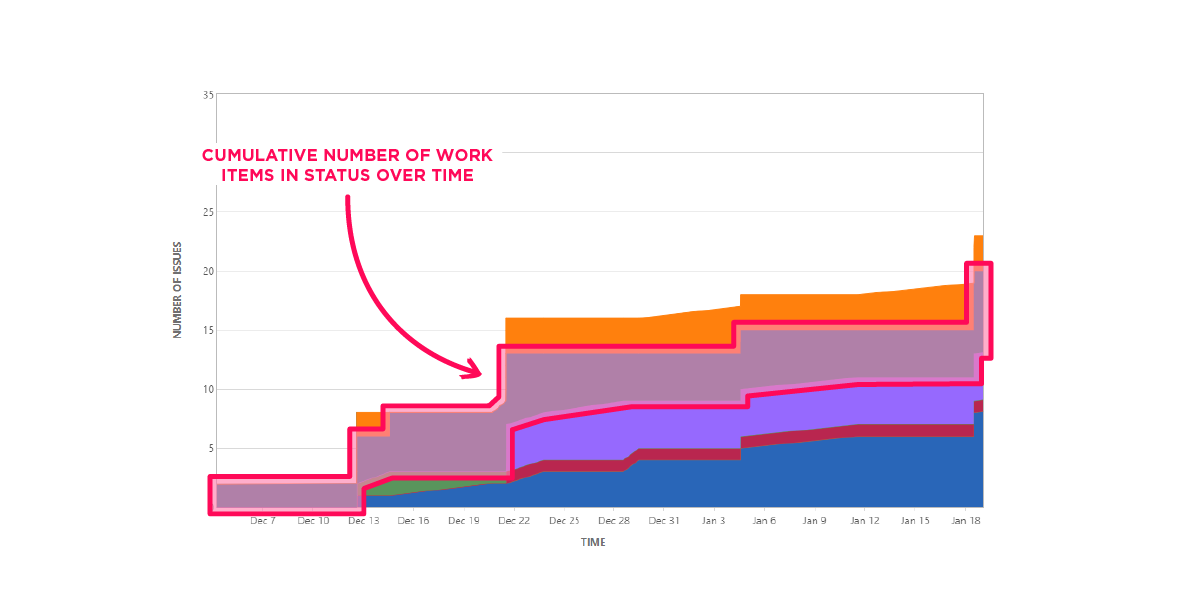
A cumulative flow diagram (CFD) is a powerful tool for visualizing the flow of work in a project. It provides a snapshot of how work is progressing at a given point in time and can help organizations identify bottlenecks, delays, and areas of the workflow causing inefficiencies.
A CFD is created by plotting the number of items in each workflow stage over time. It provides a clear visual representation of the flow of work and can help project managers identify patterns and trends in the data.
For example, a project manager may notice a trend of increasing work in progress, indicating that the team isn’t keeping up with demand.
7. Delivery Performance
Delivery performance measures the ability of a team to deliver work items within agreed-upon time frames. It’s calculated by dividing the number of completed items by the total number of items that were started within a given time period.
High delivery performance indicates that the team is able to complete work items efficiently, while low delivery performance may indicate that the team is struggling to meet customer expectations and deliver work items on time.
Delivery performance can be used to make data-driven decisions about process improvements and resource allocation. For example, if a team has low delivery performance, organizations may want to review the workflow to identify bottlenecks.
What Is the Difference Between Lead Time and Cycle Time in Kanban?
Lead time and cycle time are two key metrics in Kanban used to measure the performance of a workflow. While both metrics are important, they’re different and provide valuable information in different ways.
Lead time is the total amount of time it takes from when a customer request is made until the moment the work is delivered to the customer. It provides valuable information about the overall performance of the workflow and how well the team is able to meet customer expectations.
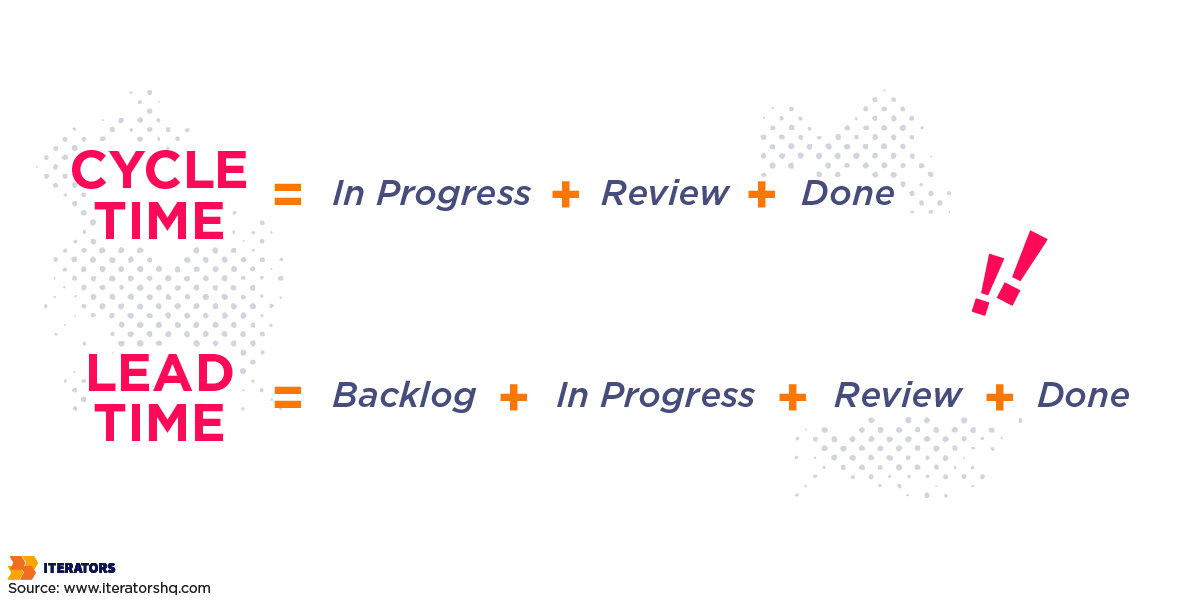
On the other hand, cycle time measures the time it takes for a work item to move from the start of the process to the end. It provides information about the efficiency of the workflow and how well the team is able to complete work items on time.
So, both lead time and cycle time are important metrics in Kanban that provide valuable information about workflow performance.
But lead time provides information about the overall performance of the workflow, while cycle time provides information about the efficiency of the workflow and how well the team is able to complete work items on time.
By tracking both lead time and cycle time, organizations can understand the workflow’s performance and make data-driven decisions to optimize the workflow and improve the delivery of projects.
How to Optimize the Kanban Method?
Optimizing the Kanban method can help you streamline your workflow, increase efficiency, and reduce waste. Whether you’re just starting with Kanban or have been using it for some time, there are several steps you can take to optimize your process.
Let’s look at two of the most effective ways to optimize the Kanban method:
1. Use Different Types of Kanban Review Meetings
A critical aspect of optimizing the Kanban method is conducting regular review meetings. These meetings serve as an opportunity to reflect on the current state of the workflow and identify areas for improvement.
There are several types of Kanban review meetings, each with its focus and purpose. Let’s take a look at them:
Daily Stand-up
A daily stand-up meeting is a short, focused meeting held at the beginning of the workday. The purpose of this meeting is to quickly align everyone on the team about what each person is working on and what help they might need from others.
Retrospective
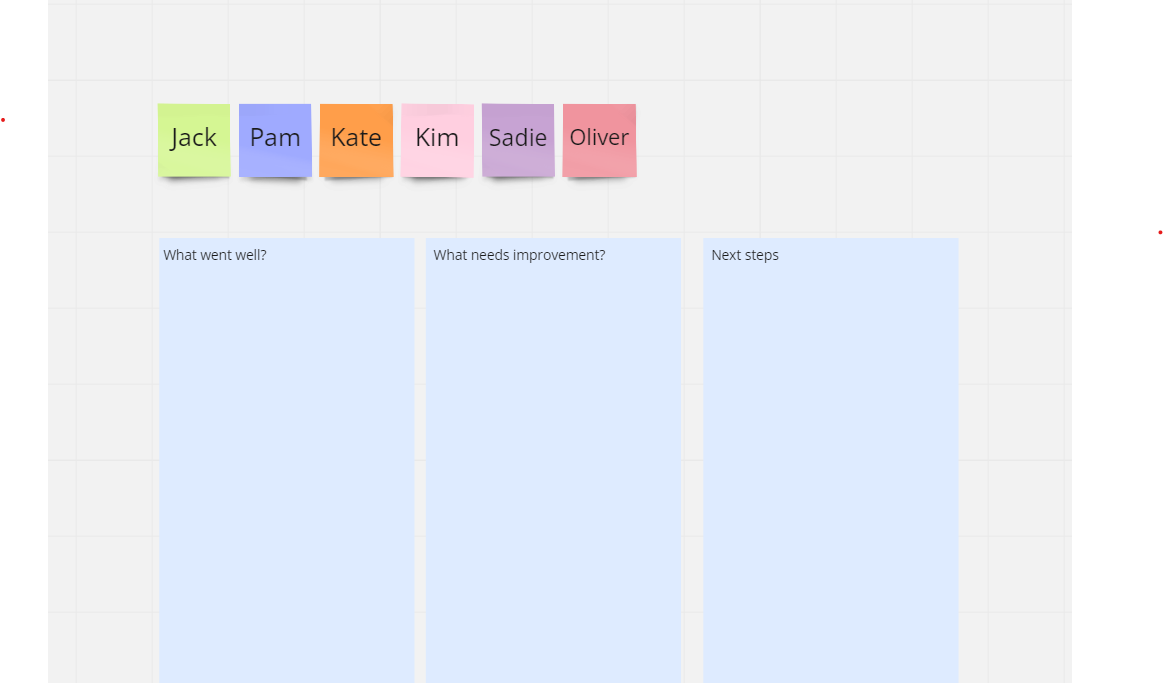
Retrospective meetings are held at the end of a project or at regular intervals during the project. The purpose of these meetings is to reflect on the project and identify areas for improvement in the process.
In a retrospective meeting, the team discusses what went well and what didn’t and creates action items for improvement.
Work-in-Progress Limit Meeting
A work-in-progress limit meeting is a regular review of the work-in-progress (WIP) limits set for each workflow stage. This meeting aims to ensure that work flows smoothly through the stages and that WIP limits are appropriate and followed.
Class of Service Meetings
Class of service (CoS) meetings are used to review the different classes of service used in the Kanban workflow. During these meetings, teams can discuss the priority of different work items and ensure they are delivered in the right order.
Replenishment Meetings
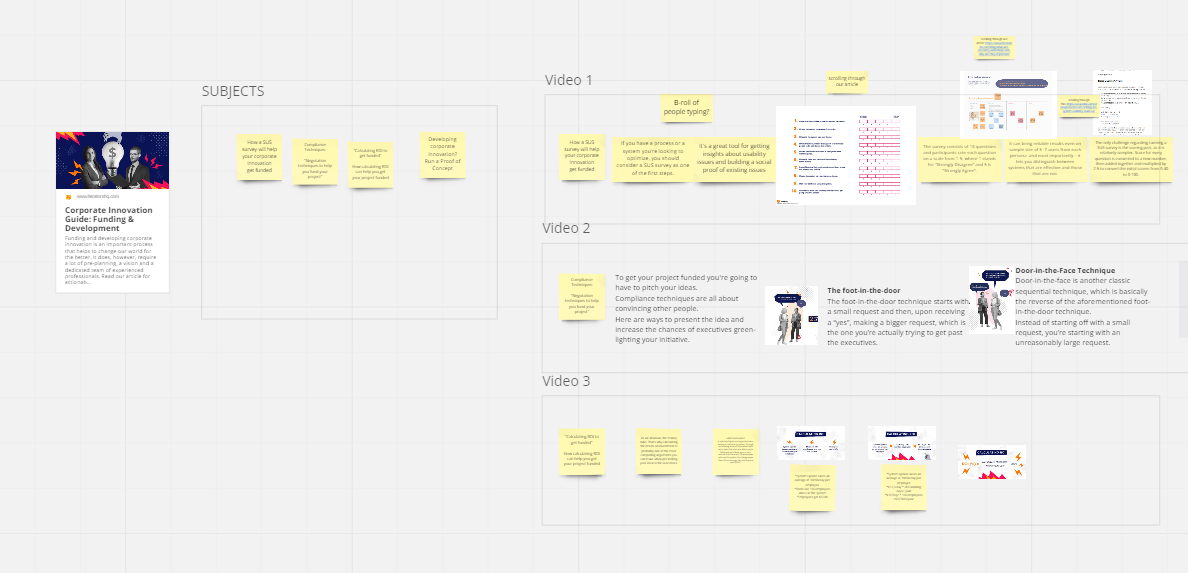
Replenishment meetings are used to review the inventory of work items available for delivery. These meetings aim to review the status of work items and decide which items should be prioritized for delivery.
Process Performance Meetings
Process performance meetings are used to review the performance of the workflow and identify areas of the process that need improvement.
During these meetings, teams can review metrics like cycle time, lead time, and delivery performance to identify areas of the process that need improvement.
Flow Efficiency Meetings
Flow efficiency meetings are used to review the efficiency of the workflow and identify areas causing inefficiencies. During these meetings, teams can review metrics such as flow efficiency to identify areas of the process that need improvement.
Each meeting type has a specific purpose and provides valuable insights into the effectiveness of your workflows. You can stay ahead of any inefficiencies or roadblocks when you conduct these meetings regularly.
2. Kanban Maturity Model
The Kanban Maturity Model (KMM), created by David J. Anderson and his team, is an effective tool for organizations looking to optimize their Kanban method implementation. It provides a roadmap for organizations looking to optimize their Kanban workflows.
By following the model, organizations can move from a basic Kanban implementation to an antifragile production process capable of responding quickly to changing demands and delivering high-quality products.
The Kanban Maturity Model provides a roadmap for improving your processes and workflows. From the initial adoption of the Kanban method to creating an efficient team, the mode is divided into four levels: adoption, initiation, evolution, and optimization.
At each stage, you’ll have specific goals to reach and metrics to track. This will allow you to identify areas of improvement and gauge your progress. By implementing the Kanban Maturity Model, you’ll better understand your workflow processes.
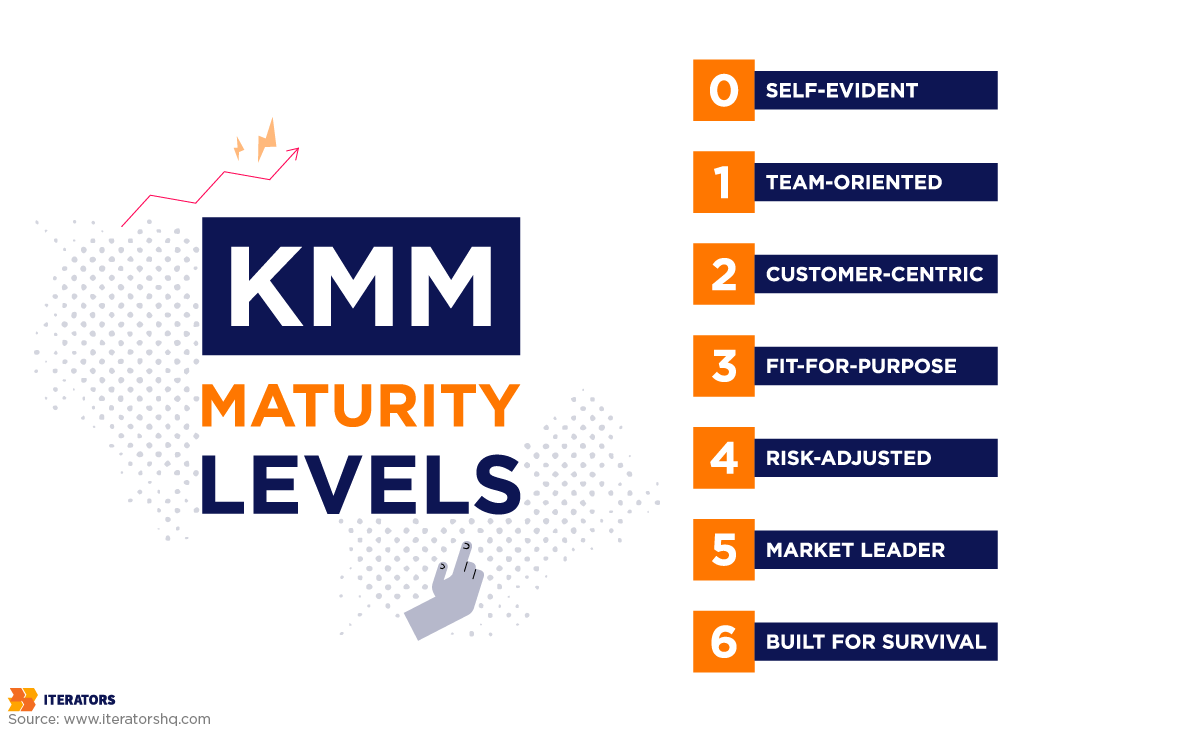
Plus, the model will help you discover new ways to achieve better results, improve workforce efficiency, reduce workflow bottlenecks, and increase time to completion.
What Is and How Can You Use the Kanban Control Chart?
A Kanban control chart is a visual representation of the flow of work items in a Kanban system. It provides a real-time overview of the system’s performance and helps identify areas of improvement.
The chart typically displays the number of work items in various stages of the process, making it easy to see how work items are flowing through the system and where bottlenecks or disruptions are occurring.
This visual representation also allows you to identify areas of improvement and make data-driven decisions to optimize your delivery process.
For instance, you can use the chart to monitor the lead time variability, wait time, and blocked time and make changes to reduce these times and improve flow efficiency.
You can also use the Kanban control chart to monitor the adherence to the WIP limit, which helps ensure the system isn’t overburdened with too many tasks in progress. Plus, with the ability to measure performance over a period of time, you can observe the impact of your continuous improvement efforts.
Moreover, you can employ the Jira Control Chart solution to evaluate your cycle time and lead time. This will allow you to make better use of time in your projects and workflow. The control chart can help you to map the cycle time to forecast future performance.
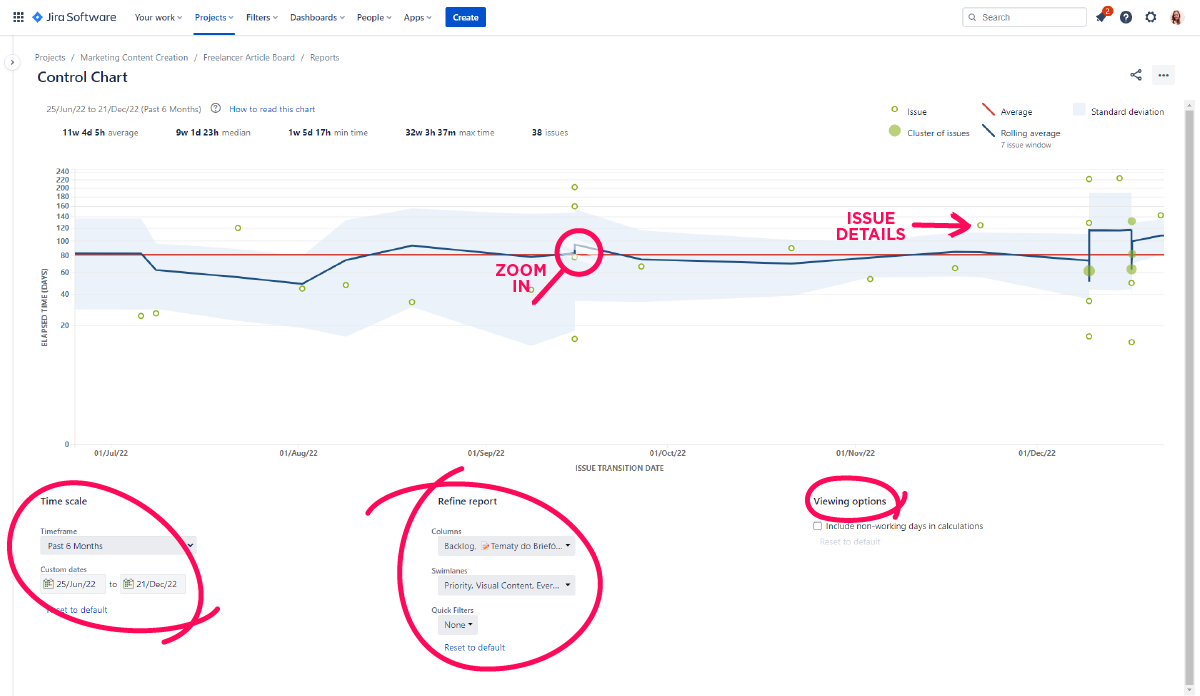
But is there a predetermined process you need to follow when using a Kanban control chart, or can you tailor the chart to your needs? Let’s check out how to create the Kanban control chart below.
Steps to Create the Kanban Control Chart

1. Accumulate Data
To create a Kanban control chart, you need to first identify the stages of your process. These stages could be anything from “To-do” to “In progress” to “Done.” The key is identifying the stages that make the most sense for your process and team.
After that, accumulate and collect information about your work processes by looking at Kanban metrics like work-in-progress, lead time, cycle time, etc. The resulting data collection will serve as the foundation for your chart.
2. Choose the Right Tool
When you have gathered your data, choose a tool to plot your data. This can be done in a spreadsheet, such as Google Sheets or Microsoft Excel. You can also use project management software or apps to plot your collected data.
Make sure to label each stage clearly, and show the workflow between stages.
3. Plot the Collected Data
Input the data into your flowcharting tool to create a graph. Make sure the time is plotted on the X-axis, and the work-in-progress is plotted on the Y-axis.
This graph will visually represent your overall work processes in a given period. It’ll also help you identify the work processes that might need improvement.
4. Analyze the Chart
After completing the chart, you can now analyze and interpret it. Try to look for patterns, trends, bottlenecks, or areas for improvement.
By analyzing the evident trends, you can determine what changes you need to make to improve your workflows.
5. Execute the Changes
Based on your chart analysis, execute and implement the changes. Create a plan to make improvement efforts to optimize your workflow continuously. This may include changes to tools, processes, or how the work might be performed.
Plus, when executing the changes, remember that your ultimate goal should be to create a more streamlined and efficient work environment.
How to Use a Kanban Control Chart to Improve your Process?
A Kanban control chart can be a powerful tool in helping you track work progress over time and monitor the effectiveness of your process improvement efforts. Now that we know how to make the chart, let’s look at how you can use it to improve your process:
- Monitor and Measure Performance – Once you’ve set up the chart, continuously monitor and measure the performance of your delivery process.
- Identify Areas for Improvement – Use the insights from the Kanban control chart to identify areas for improvement in your process.
- Make Data-Driven Decisions – Using insights from the Kanban control chart, make data-driven decisions.
- Implement Changes and Assess Impact – Implement the changes and assess the impact on the delivery process. You should also continuously monitor and measure the performance of the process to see if the changes have had the desired effect.
The Takeaway
Kanban metrics provide valuable insights into the performance of your production process and can be used to identify areas for improvement.
By using these metrics in combination with other lean production techniques, such as the Kanban Maturity Model (KMM), you can optimize your Kanban workflows and improve your overall efficiency.
Similarly, you can create Kanban control charts to track your production processes’ performance and identify improvement areas. They’ll help you identify and address the causes of disruptions, improving workflows and reducing wait times.
So, if you want to improve your workflow, track progress, identify bottlenecks or delays, prioritize the most critical tasks, and achieve the best workflow results and outcomes, Kanban metrics might be what you’re looking for.